Zuverlässigkeit und Sicherheit moderner Karosseriestrukturen
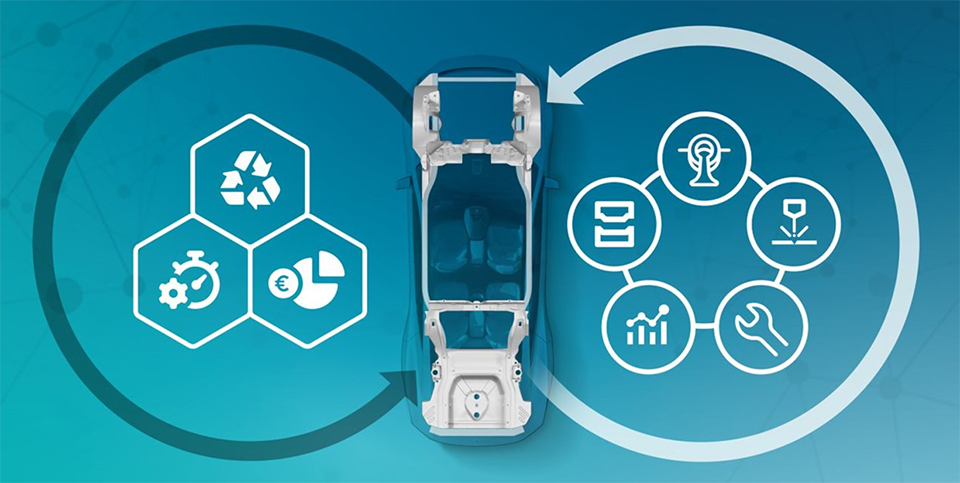
Das Leitprojekt »FutureCarProduction« fokussiert auf den Leitmarkt Mobilität und erarbeitet Lösungen für nachhaltige und innovative Karosseriekonzepte, die über den aktuellen Trend des Giga-Castings weit hinausgehen. Acht Fraunhofer-Institute gehen dabei der Frage nach, wie Fertigungskonzepte für Karosserien mit modernsten Füge- und Gießtechnologien hinsichtlich der Effekte auf Nachhaltigkeit und Kreislauffähigkeit bewertet werden können, um Ressourcen zu schonen und Effizienz sowie Leistungsfähigkeit zu steigern.
Der Karosseriebau für Pkws unterliegt einem Wandel, der von zwei bedeutenden Einflüssen geprägt ist. Hierzu zählt die Entwicklung neuer Karosseriebauweisen basierend auf hoch integrierten Großgussteilen, im Sinne des »Giga-Casting«, die zu Einsparpotenzialen in der Lieferkette führen sollen sowie die Umsetzung eines nachhaltigen und klimaneutralen Automobilbaus bis 2050.
Hier setzt das Leitprojekt »FutureCarProduction« mit einer herausragenden Innovation als Ziel an: Die Entwicklung neuer Fertigungsprozesse auf Basis des Verbundgusses »FusionCASTING®« zur Erzielung hochintegrierter Karosseriestrukturen aus Blechumform-, Füge- und Gussstrukturen einerseits sowie andererseits die Etablierung von ganzheitlichen Lösungsansätzen zur Bewertung von Karosseriekonzepte nach Nachhaltigkeit, technischer Performance und Kosten. »FutureCarProduction« leistet mit einer ganzheitlichen Methoden- und Technologieentwicklung einen wichtigen Beitrag leisten, um Unternehmen bereits in einer frühen Phase im Entwicklungsprozess zu befähigen, robuste Entscheidungen bei der Entwicklung neuer Karosseriekonzepte zu treffen. Der Lösungsansatz des Gesamtprojektes umfasst dazu eine methodenbasierte Analyse und Bewertung von Fahrzeug- bzw. Karosseriearchitekturen unter Berücksichtigung von konventionellen und neuartigen Fertigungsprozessen (Gießen, Umformen, Fügen) sowie den nachhaltigen Materialeinsatz durch die Erhöhung von Recyclingmaterial.
Die Aufgabe des Fraunhofer LBF im Rahmen des Vorhabens ist es, die Sicherheit und Zuverlässigkeit sowie die Performance von Karosseriestrukturen zu gestalten sowie diese, insbesondere beim Einsatz von Recyclingmaterial, untereinander bewertbar zu machen. Dabei greifen numerische wie auch experimentelle Simulationsmethoden ineinander, um die zu entwickelnden Verbundgussstrukturen bezüglich Leichtbau, Lebensdauer, Schädigungsfortschritt und Sicherheit optimal auf den Anwendungsfall in der jeweiligen Fahrzeugarchitektur abzustimmen. Dies schließt die Auswahl der anwendungsbezogen, richtigen Karosseriefertigungsmethode mit ein, welche die höchste Nachhaltigkeit und Zuverlässigkeit bei geringsten Kosten abbildet.
Dabei werden grundlagenorientierte Methoden zur Festigkeitssimulation von Fügeverbindungen aus Strukturguss-Blech sowie Strangguss-Blech entwickelt, die die Gestaltung von Zuverlässigkeit und Sicherheit dieser Fügeverbindungen ermöglichen sowie den Einfluss von Recyclingmaterial auf die Zuverlässigkeit bewerten können. Für eine ganzheitliche Betrachtung neben nur klassische Blechbauweisen in Kombination mit Stranggussprofilen, Multimaterialverbünden auf Basis von Schweiß- und Nietprozessen untersucht, sondern im Wesentlichen Fraunhofer-eigene Ansätze über den Verbundguss »FusionCASTING®« als hochintegrative Fertigungsmöglichkeit als Kombination von Strukturguss-, Stranggussprofilen und Schweiß-/Nietstrukturen gestaltet und bewertet. Die Ergebnisse des Teilprojektes ermöglichen einen weitreichenden und schnellen Einsatz im Automobilbau, um für spezifische Fahrzeugarchitekturen die jeweils optimale Karosseriefertigungsmethode auswählen zu können.