HiL basierte Testumgebung für Traktionsbatterien
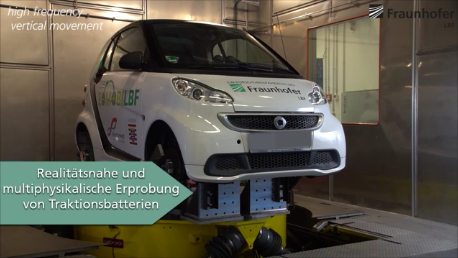
Realitätsnahe Prüfung, Fahrsimulation, Fahrzeugmodelle
Traktionsbatterien sind sicherheitsrelevante Bauteile, die elektrischen, mechanischen und thermischen Belastungen während des Betriebs unterliegen. Die Validierung und Absicherung von Batterien werden derzeit noch als sequenzieller Prozess im Labor durchgeführt. Es werden lediglich die einzelnen Belastungsdomänen in standardisierten Laborversuchen abgebildet. Der Systemtests erfolgt jedoch erst an fahrenden Fahrzeugprototypen. Dieser Prozess ist sehr kosten- und zeitaufwändig, insbesondere wenn Probleme erst im finalen Integrationstest auf Gesamtfahrzeugebene auftreten und somit die gesamte Entwicklungs- und Testschleife neu durchlaufen werden muss. Des Weiteren ist der Realitätsbezug des Testszenarios bei solchen konventionellen Prüfungen im Labor vergleichsweise gering. Zusätzlich ist die Absicherung von unterschiedlichen Fahrzeugderivaten und Testszenarien (d.h. Manövern, Rand- sowie Umweltbedingungen usw.) durch die Anzahl an Prototypenfahrzeugen und durch sicherheitsrelevante Aspekte beschränkt.
Um diese Einschränkungen zu überwinden, haben wir am Fraunhofer LBF eine auf realen Manövern basierte Hardware-in-the-Loop (HiL) Testumgebung für Traktionsbatterien entwickelt. Sie basiert auf der Integration einer detaillierten dynamischen Fahrzeugsimulation in einen multiphysikalischen Batterieprüfstand, der mechanische, elektrische und thermische Erprobungsbedingungen gewährleistet. Unser Projektteam hat ein echtzeitfähiges modulares Fahrzeugsimulationsmodell entwickelt, um die multiphysikalischen Belastungen, die im realen Fahrbetrieb auf eine Traktionsbatterie wirken, in Echtzeit zu generieren und auf den Batterieprüfling am Prüfstand einzuleiten. Dafür benötigt die Fahrzeugsimulation die Zustandsgrößen der Batterie, die durch eine HiL-Schleife als Feedback ins numerische Simulationsmodell zurückgeliefert werden. Als reale Manöver werden Verbrauchszyklen (NEFZ, WLTC usw.), Fahrdynamikmanöver und Betriebsfestigkeitsmanöver (Schlechtweg, Schlaglochüberfahrt usw.) simuliert.
Die entwickelte Testumgebung erlaubt eine progressive Integration der Hardware-Komponenten (d.h. Batterie und Prüfstand) in eine Plattform basierend auf numerischer Simulation. In der ersten Stufe werden Simulationsmodelle der Batterie und des Prüfstands mit der Fahrzeugsimulation gekoppelt, um erste rein numerische Konzeptanalysen auf einer Workstation durchzuführen. In der zweiten Stufe wird die Systemsimulation auf der Ziel-HiL-Hardware mit realen I/O-Kommunikationsschnittstellen durchgeführt, um die Echtzeitfähigkeit der Applikation und die Signalschnittstellen zu testen. Danach wird die elektrische Domain der Prüfung integriert, wobei die Batterie und ein elektrischer HV-Prüfstand physikalisch vorhanden sind und mit HiL angebunden werden. In der finalen Integrationsstufe werden auch die mechanische und thermische Domäne in den multiphysikalischen Prüfstand integriert.
Mit dem entwickelten Ansatz ist es möglich, multiphysikalische Belastungen für unterschiedliche, virtuelle Fahrzeuge zu generieren, um die realitätsnahe Erprobung des Batterieprüflings für entsprechende Fahrzeugderivate ohne physikalische Fahrzeugprototypen im Labor experimentell durchzuführen. Extreme Testszenarien sind mit einem hohen Maß an Reproduzierbarkeit, Machbarkeit und Sicherheit realisierbar. Die Digitalisierung einzelner Schritte im Absicherungsprozess ermöglicht es, diesen modular aufzubauen sowie zu verkürzen. Somit wird die Entwicklung für den Batteriehersteller und den OEM deutlich ökonomischer.