Challenge: highly loaded structural components with weld lines
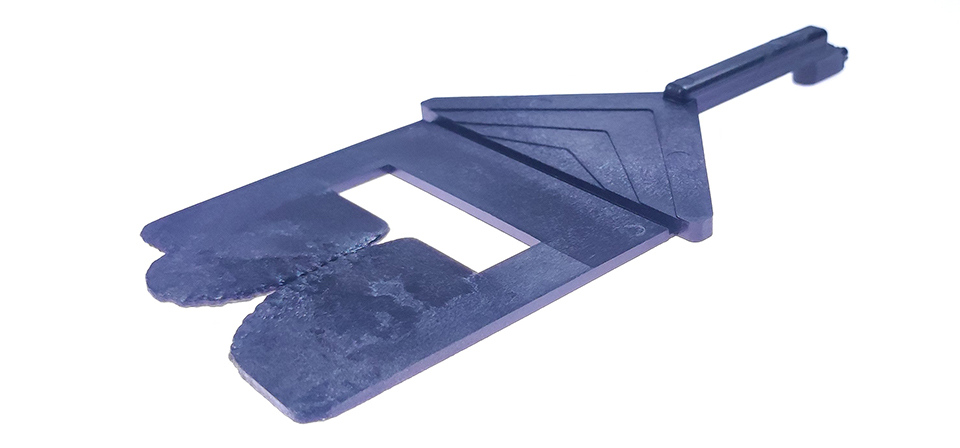
Due to the integration of functions and lightweight design, weld lines are present in almost all technical components. In the design process, numerical simulation methods or empirical values are used in an attempt to relocate weld lines to less heavily loaded or invisible component areas. However, this is not always successful as desired, because external influences such as the rheology of the melt, process parameter or component geometry often cause the weld line to shift to non-predetermined, critical or failure-relevant component areas. If you only become aware of this during component sampling or during the release test due to premature damage, the start of production and product lauch can usually no longer be met. At such an advanced stage of component approval, changes to the gating system or component design are only possible at great expense in terms of time and money.
In particular, the increased use of recyclates due to the EU's ELV-Regulation makes the reliability and lifetime assessment of recyclates a particular challenge. Due to the material mix and previous history, recyclates exhibit a greater range of variation in rheological, morphological and process properties, which are a particular challenge for weld lines.
The following research questions are intended to investigate the fundamental interactions between rheological, morphological, process and long-term properties in highly loaded applications:
By understanding the interactions between rheology, morphology and process, weld lines can be better evaluated in terms of their reliability and long-term properties. You can acquire this expertise in this joint industrial project ‘Design for Reliability - weld lines in structural components’. Take part and benefit from the expertise of Fraunhofer LBF.
Basic literature research and evaluation
Based on the materials selected in the composite (e.g. PP, rPP, PA6, rPA6 or PPA) and taking into account their fillers and reinforcing materials, a research of available materials is carried out. For this purpose, the material property profiles and the expected weld line quality are compiled and initial resulting challenges are derived.
Determination of the rheological and morphological properties to assess the application-specific suitability and weld line quality
Analytical tests are used to determine the actual state with regard to the rheological and morphological material properties. These are used for evaluation and description, as well as the derivation of process parameters for good or poor weld line quality.
Investigating the long-term properties
Using an injection moulding tool with special inserts, test specimens with a weld line are produced at the Fraunhofer LBF. Process parameters are to be specifically influenced in such a way that ‘good’ and ‘poor’ weld line properties result. The interaction of the notch effect (shape of the moulded core) on the static and cyclic long-term properties will be specifically investigated.
Microscopic and macroscopic morphology in the weld line
Special attention will be paid to the microscopic and macroscopic morphology in the weld line. Microscopically, the area of the weld line will be examined using µ-CT and microscopy for the local fibre orientation and confluence of the melt flow fronts. Macroscopically, the crack initiation and crack propagation as well as the damage pattern under static and cyclic loading will be analysed.
Derivation of a catalogue of measures
The material properties determined from rheology, mechanics and microscopic and macroscopic morphology are incorporated into a catalogue of measures for reliability assessment of weld lines. With this catalogue of measures, the partners are able to better evaluate the process parameters, long-term properties and reliability and become aware of critical conditions and areas of the weld line in the early phase of product development.
The participating partners are thus able to address their requirements specifically to material suppliers, manufacturers and subcontractors and have the opportunity to adapt their material formulations, component design or process parameters in line with requirements.
Participating partners in this joint project will be able to
This joint project is aimed at companies along the value chain from the granulate to the component: