Know independencies, reduce costs
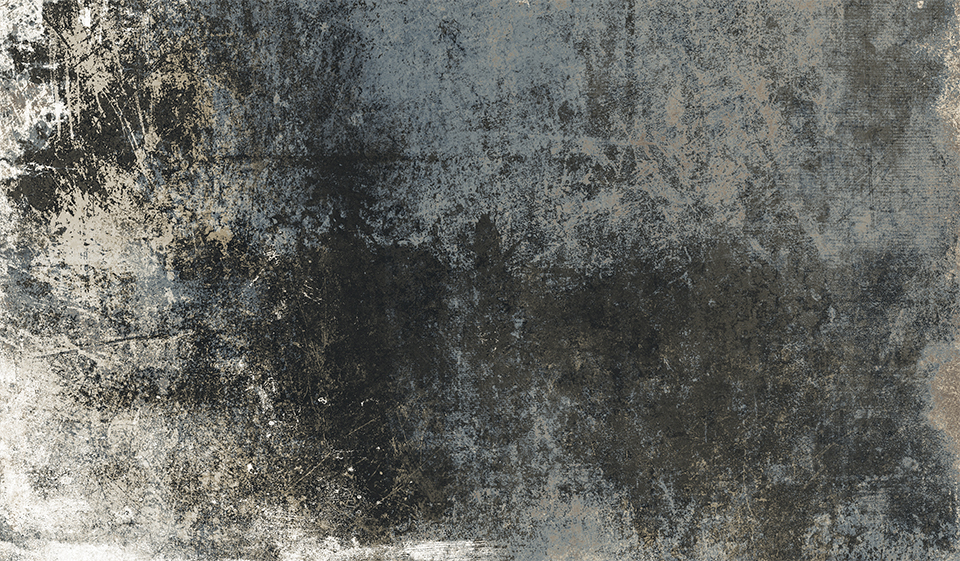
The composition of recycled plastics fluctuates from batch to batch. In addition to the changing properties of the recyclates, impurities also have to be dealt with. These can accumulate in the recyclate despite the melt filtration during the regranulation step. According to reports from recyclate processors, this can lead to the formation of massive deposits on the mould surfaces and an increase in demoulding forces, which ultimately results in damage to the injection-moulded parts.
Increasingly thicker deposits reduce the component quality regardless of the demoulding forces due to the deviating geometry. In addition, the deposits can lead to corrosion of the mould steel. Additional cleaning intervals are necessary to counteract the effects of the deposits described above. These and any increased wear that may still occur will result in additional costs for processors. Exact dependencies are not currently known.
The purpose of the joint research project is to support the participants in achieving smooth processing of recycled materials. Measures to suppress deposit formation shall be developed, and a thorough insight into the melt-steel interactions during the processing of recyclates be gained.
Recyclate manufacturers and plastics processors will take immediate benefit by the project. It will be also interesting for steel coaters. Welcome are all partners along the value chain who are interested in recyclate processing.
Deposit formation, demoulding forces and wear caused at the tool steels by corrosive and abrasive plastics melts has been a field of work at the LBF for quite some time. We will focus on injection moulding tests with varying process parameters and carry out accompanying characterisations.
At the beginning, a comprehensive literature study on the processing of recycled materials shall be conducted. In the experimental work the process and material parameters with a particularly high damage potential, i.e. those that lead to a pronounced reduction in service life of the mould equipment, are to be identified testing a larger number of recyclate batches. The detailed experimental plan will be developed together with the participants and if necessary, be adjusted in course of the project in close consultation.
A special mould developed at the LBF equipped with force transducers enables recording of the demoulding force during the demoulding of a test specimen in high temporal resolution.
During the deposit formation, the demoulding force profile changes over time, making it possible to detect the deposits and their effects (e.g. increase in demoulding force) at an early stage. This in turn enables a higher number of trials (with different moulding compounds and process parameters) within a given time frame. The injection moulding tool also has interchangeable inserts so that different steels can also be tested
Accompanying characterizations will be performed, such as:
Combining all the test results, ways to avoid/reduce the formation of deposits shall be explored (e.g. mixing with virgin material, using processing aids etc.). This includes the development of an assessment tool for rapid estimating the damage potential of a given batch by easy-to-use methods.