Accelerated cost-optimized compound development
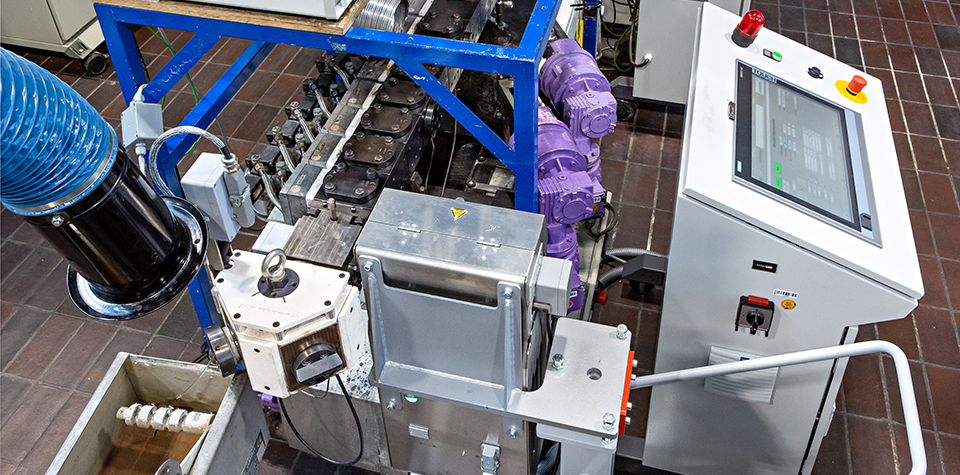
In the plastics industry, as in many others, there is increasing pressure to carry out R&D activities in ever shorter times and at lower cost. At the same time, in production it is important to reduce scrap rates and avoid bad batches in order to conserve resources and reduce costs.
One example is process stabilization. When developing new plastic compounds, the process stabilization must be optimized regarding cost/benefit considering resource conservation and economic efficiency. Up to now, experimental compounds with different amounts of antioxidants have been prepared in the form of concentration series. These are then characterized offline using various tests, such as measuring the volume flow rate (MVR, DIN 1133-1). Reliable results are therefore only obtained after the compounding step. This is a lengthy process. The issue of process stabilization arises in the compounding of both virgin and recycled materials.
Online rheology, operated on the compounder between the screw tips and the strand die, is a promising tool to assist in this situation. The compounder can be a test machine for development or a large production machine. An initial study at the LBF demonstrated the potential of online rheology for process stabilization (Plastics Insights 7 (2023) 67-69).
In general, rheological variables such as shear rate dependent shear and extensional viscosity are in many cases highly sensitive to changes in melt properties and hence the resulting material properties. The extensional rheometer (LDR, Leistritz) allows the two viscosities to be measured simultaneously as a function of shear rate, resp. strain rate (for elongational viscosity). It has a slotted channel die that can also be used to measure filled compounds, such as glass fiber compounds. This makes it very flexible.
The proposed joint research project will enable participants to carry out accelerated, cost-optimized compound development based on defined model studies and to evaluate them for their specific applications. Another objective is to assist the project partners in their assessment of the benefits that can be achieved by an online rheometer. It is also expected to provide insights into the influence of batch and process variations on the properties of injection molded parts. This can help to reduce the need for offline analysis.
The following topics may be considered for model studies:
At the beginning of the project, the questions to be addressed in the project are identified with the project partners. The plastic grades and additives to be processed as model materials for each question, as well as the concentration ranges and processing conditions, are also determined.
During compounding trials, concentration series of the relevant additives or fillers are run, and shear and extension viscosity flow curves are measured for each composition.
To obtain comparative data, the test compounds are analyzed off-line. Based on the above examples for positions 1-3, the molecular mass distribution is determined by GPC. For example, at position 4, the actual filler content of the test compounds is determined by ashing. When questions arise about filler content or the processing of recyclates, injection molding trials are also carried out, followed by appropriate tests to determine the specific impact of batch variations on component properties.
Finally, the significance of the correlation between the rheo-curves and the offline findings is assessed. Chemometric methods may also be used where appropriate.
All results will be discussed with the group of participants. A final report will be prepared.